Developing a pick and place application involves careful consideration of various components, including the selection of the robot and gripper. This guide explores best practices, key considerations, and technical details necessary for successful deployment of a pick-and-place application.
We'll use OnRobot's lineup as a reference due to their comprehensive suite of flexible grippers, quick deployment, and reduced programming time - all ideal for pick-and-place applications.
Selection of the right gripper, the critical interface between the robot and the task, is paramount. Here are the key factors you should consider:
- Workpiece Shape
- The shape of the workpiece determines the type of grip needed. Different shapes may require different gripping mechanisms to securely handle the object without causing damage or slippage.
- Example: A cylindrical object might be best handled by a three-finger gripper, while a flat object might require a vacuum or suction gripper.
- The shape of the workpiece determines the type of grip needed. Different shapes may require different gripping mechanisms to securely handle the object without causing damage or slippage.
- Workpiece Weight
- The weight of the item affects the gripper's design and strength. Choosing a gripper that can handle the weight ensures stable and safe operation without overloading the robotic system.
- Example: Heavier objects require grippers with higher payload capacity, ensuring they can be lifted and moved without mechanical failure or loss of precision.
- Workpiece Size
- Size influences the gripper's reach and the amount of force it needs to apply. A mismatch in size can lead to inefficient handling or inability to grip the object effectively.
- Example: Large objects might need a gripper with a wider opening and more substantial gripping force, while small objects require precision and delicate handling.
- Workpiece Material
- The material of the workpiece dictates the gripper's material compatibility, ensuring that the gripper does not damage the object during handling.
- Example: Soft or delicate materials might need grippers with softer contact surfaces or adjustable gripping force to avoid damage, while hard materials like metal might need more robust grippers.
There are many different types of grippers out on the market. We'll cover some of the main categories below that are used for typical pick and place applications for the majority of part geometries.
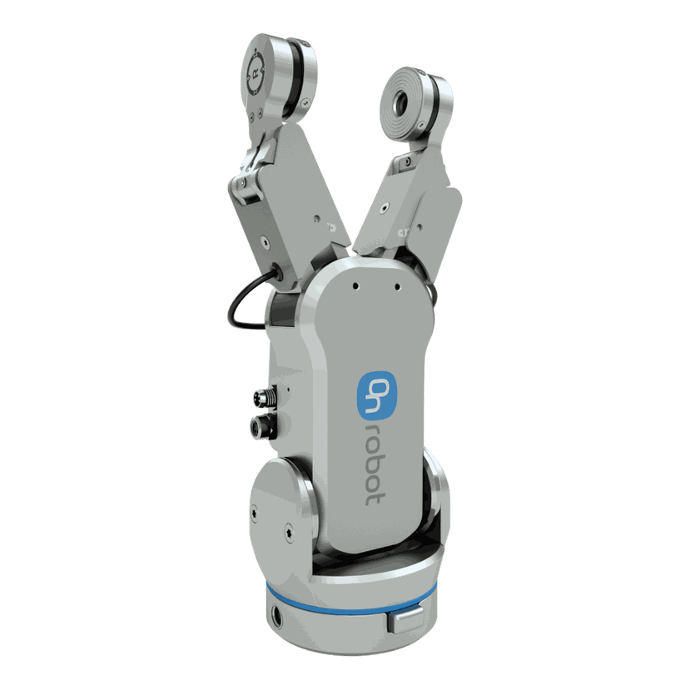
Finger grippers
These are ideal for diverse product ranges due to their programmable gripping forces and widths. RG2 and RG6 two-finger grippers and RG2FT grippers, for delicate parts requiring precise forces, are some excellent examples.
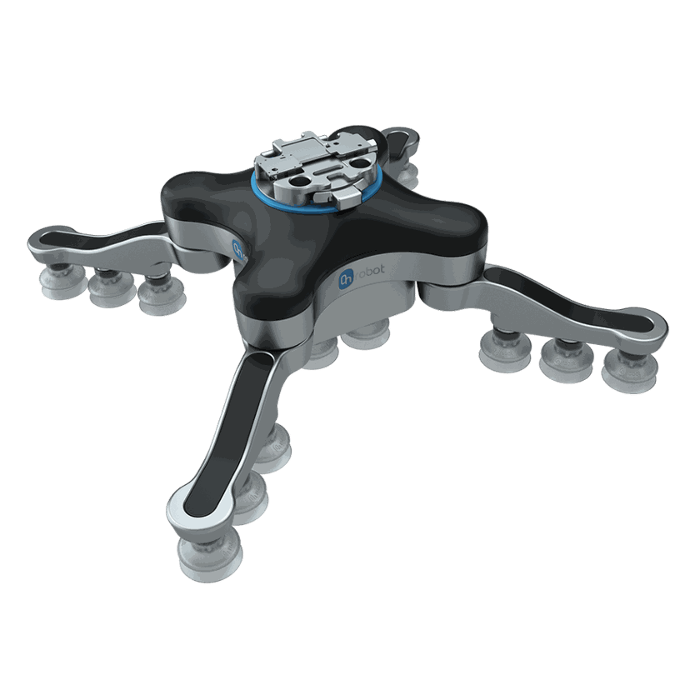
Vacuum Grippers
OnRobot’s electric vacuum grippers, including VG10, VGC10, and VGP20, offer versatility and reliability, making them perfect for various pick-and-place applications.
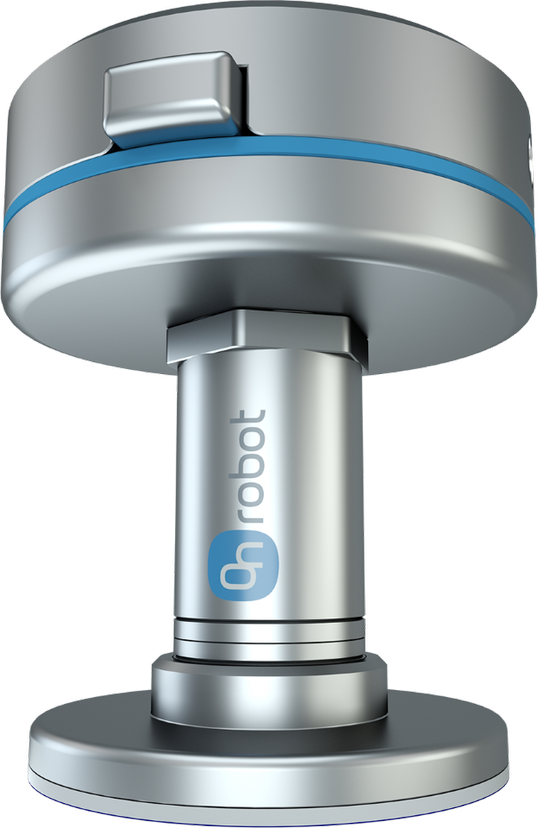
Specialized Grippers
Certain products require specialized grippers for optimal performance, like MG10 magnetic grippers for ferromagnetic parts and Gecko Single Pad Grippers for flat, smooth, or perforated objects..
Finally, you should decide if your pick and place application requires a single or dual gripper configuration. A dual setup can reduce cycle time, but it also adds complexity to the robot programming. You can see a video of what a dual gripper from OnRobot looks like in this video showing a packaging application with OnRobot and Universal Robots
In Part 2 of this blog series, we will cover robot selection for pick and place applications, and infeed and outfeed strategies for part positioning and more. If you would like to get started with automating an application, reach out to our team and we'll be happy to help.
Building a Pick and Place Application